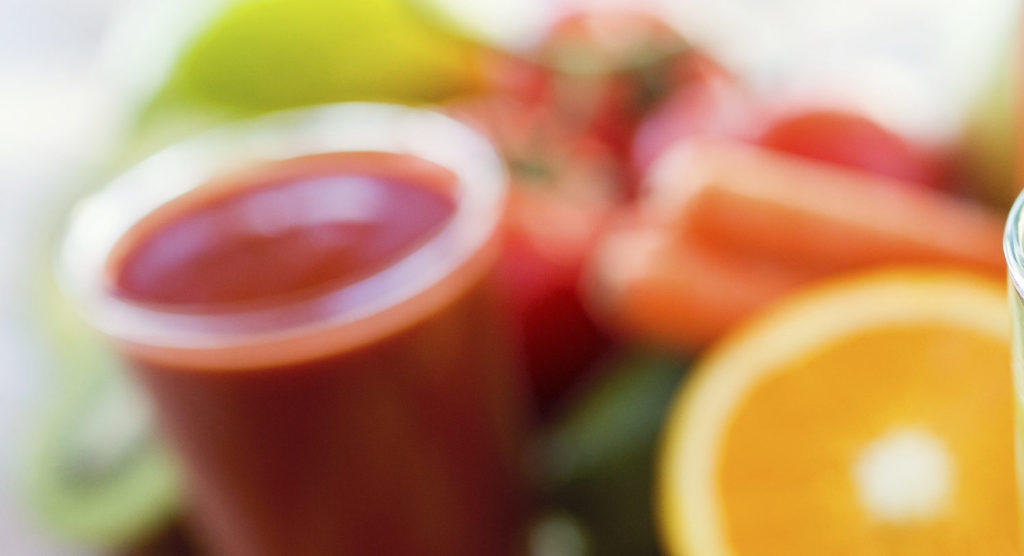
Any business trading in consumer goods should be aware of the current legal requirements and industry standards which its products must meet, as well as the risks faced if products fail to meet those standards, or worse, present risk to consumers. In a number of circumstances businesses will be directly liable to consumers where substandard products have been supplied.
The risks of product liability are heightened in the food and drink industry, with substandard consumables potentially presenting direct risk to consumers’ health and consumers being understandably more sensitive to lapses in standards. Incidents largely influence consumer confidence in the supplier and can be a major reputational risk. Maintaining standards in the food and drink industry is a particular challenge with supply chains often being lengthy and difficult to monitor.
In light of this, what can be done to mitigate risk?
Food mapping and supplier audits
To confidently say a product is ‘food safe’ requires absolute knowledge of the product’s origin and process at every stage of the supply chain. Food mapping enables producers to easily identify the stages in supply which have contributed towards the final product, and helps identify where carrying out a supplier audit may be beneficial. Food mapping can also add value to the product with consumers increasingly placing value on known origin and higher welfare.
Quality control procedures
Implementing tight quality control procedures is absolutely key to sift out substandard products and any ‘bad eggs’ so to speak. Again, the merits of quality control procedures can be drawn into the different stages of the supply chain so that quality is measured along the way. This should be discussed with suppliers prior to entering into the supply contract and is certainly something to include in supply audits.
Warranties
When entering into a supply of goods contract the buyer’s position can be greatly improved by negotiating warranties and express contractual rights. These might relate to compliance with quality procedures, compliance with industry standards and regulation, rights to audit and information regarding raw materials. Supply contracts should be carefully negotiated; spending time negotiating key terms can reduce the risk of substandard products making their way into the supply chain and help properly apportion legal responsibility where there is problem.
Contingency planning
Where incidents do happen, the impact can be carefully managed with prior planning. Small changes, such as ensuring a clear complaints procedure is in place, can make a significant difference to managing on-going relationships with consumers and avoiding losing customers. Drawing up detailed contingency plans for differing scenarios is a valuable exercise. These might include product recall procedures, deep cleaning processes where systems have been contaminated and public relations planning.
Whilst there is absolutely no replacement for (a) clear understanding and evidence of product provenance and (b) effective quality control; appropriate purchase and supply terms can be a valuable way of protecting your business against someone else’s failings.
If you have any questions with regards to this article, please contact 01392 210700 or email corporate.exeter@stephens-scown.co.uk.